US researchers working with SHoP Architects have created a potential alternative to steel and concrete as a structural floor material: recyclable panels made entirely from bioplastic and wood flour.
The prefabricated panel was made using 3D printing by researchers at the US Department of Energy’s Oak Ridge National Laboratory (ORNL) and the University of Maine (UMaine) – both part of the SM2ART public-private partership.
According to the team, the SM2ART Nfloor cassette panel is better for the environment and quicker to manufacture than similar steel-and-concrete elements, which are typically used in multi-storey buildings.
The researchers began work on the cassette following a prompt from SHoP Architects to explore the potential of bio-based materials and additive manufacturing for mass-produced floor panels.
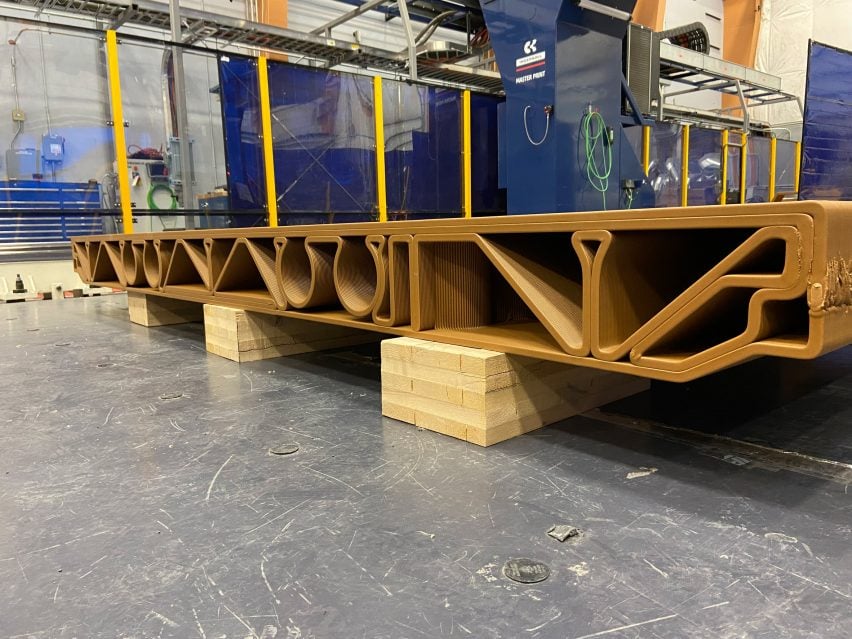
“We saw the precedent in the aerospace industry, where they introduce new technologies within small parts and expand outward to the whole,” SHoP principal John Cerone told Dezeen.
“We applied that principle by isolating a building system product — a light-gauge steel floor cassette assembly — from an existing supply-chain partner to benchmark its replacement with a single solid-state, printed, bio-based part.”
Strength from combining materials
ORNL and UMaine made the panels using polylatic acid (PLA), a bioplastic derived from corn residue, which they mixed with wood flour made from lumber processing waste.
According to ORNL researcher Katie Copenhaver, the floor panel’s strength comes from the combination of these two materials as well as its geometric shape, which distributes load to its outer edges, where it would rest within a building’s steel framework.
“Adding wood flour to the PLA increases its stiffness significantly,” said Copenhaver, with stiffness being key to the overall performance.
“What we can’t achieve with material properties alone, we can account for with structural design,” she continued. “A flat plate of steel may suffice for something and couldn’t be replaced with the same geometry of PLA, but a PLA piece could potentially be designed that could also do the job.”
According to the team’s testing, the cassette has the same strength as a typical steel-concrete floor fabrication, and they also say it is biodegradable and nicer to walk on.
Its single-piece monomaterial construction is also important. Unlike a conventional steel floor cassette, which Copenhaver said is made from 31 parts and three materials, this is quicker to make and easier to recycle.
Looking at 3D printing “in terms of performance”
The channels for wiring, plumbing and ductwork can be printed during the manufacturing process, removing the need to cut those out after assembly is completed, and so saving time and money.
The cassette took about 30 hours to print and is estimated to cut down on labour by about 33 per cent.
“When people think of 3D printing, they are usually thinking of form, or in terms of an aesthetic or formal gesture,” said Cerone. “Here, we are thinking of it in terms of performance.”
“Beyond the carbon reduction inherent in bio-based materials, leveraging additive manufacturing allowed efficient placement of structural material while integrating routes for mechanical, electrical and plumbing systems.”
While the cassette is still in the early stages of development, both the researchers and SHoP Architects believe it holds significant promise for advancing the use of organic materials in construction, particularly for modular multiresidential buildings.
The PLA and wood flour blend could be used for producing many kinds of large-format additively manufactured parts.
“What’s really exciting about this advancement is that it is industrialising a process itself, which will be applicable across all typologies and scales in the future, creating more efficient and performance-driven possibilities in everyday construction,” said SHoP founding principal Christopher Sharples.
The researchers are now working to refine the design to reduce print time and material usage, and to explore additional functionality.
SHoP Architects is based in New York City and best known for its projects in that region. These include the super-skinny Steinway Tower as well as the Brooklyn Tower – the tallest building in Brooklyn.