The European Space Agency has created its own version of a Lego brick that is 3D printed from meteorite dust, as the organisation explores how to construct buildings in space.
The “space bricks”, as Lego and the European Space Agency (ESA) call them, are made using the dust of a 4.5 billion-year-old meteorite discovered in 2000 in north-west Africa.
The meteorite dust acts as a stand-in for lunar regolith – the loose material covering the surface of Earth’s moon, which is largely the product of meteorite impacts.
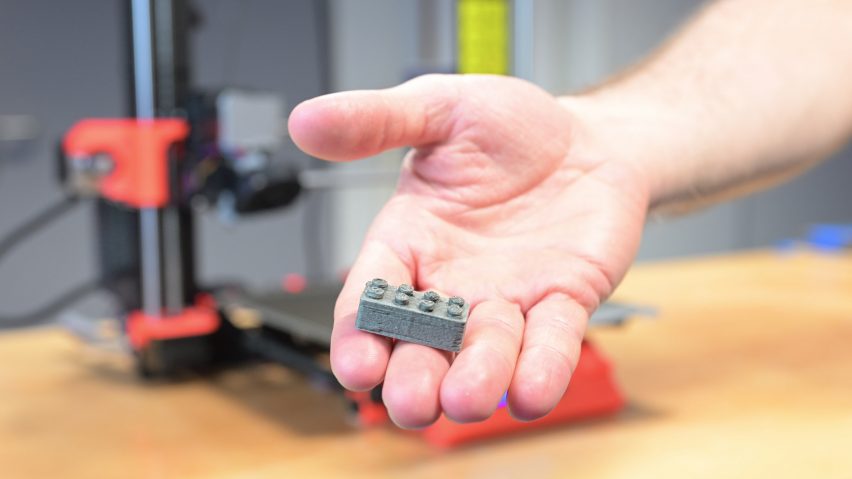
Because only a small amount of regolith exists on Earth – samples brought back during the Apollo missions – the scientists settled on the closest substitute they could find.
The space brick development is part of the ESA’s contribution to the international Artemis programme, which aims to not only return astronauts to the moon but also establish a lunar base there.
Since bringing materials from Earth is considered too expensive and time-consuming, the hope is that lunar regolith can be used to build structures such as launch pads and habitats.
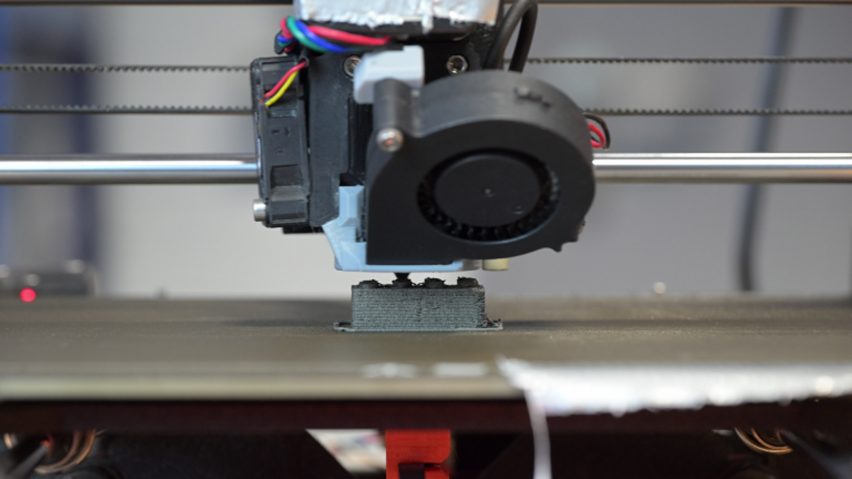
In the field of space exploration, this is known as In-Situ Resource Utilisation (ISRU) and is the focus of the ESA’s Spaceship EAC team, based out of Cologne, Germany.
ESA science officer Aidan Cowley, who heads the lab, said that his team loved “creative construction” and had the idea to explore whether space dust could be formed into a small block similar to a Lego brick so they could test different building techniques.
Our teams are working towards the future of space travel and take inspiration from not just what’s above us, but also what we can find on Earth,” said Cowley.
“No one has ever built a structure on the moon, so we have to work out not only how we build them but what we build them out of as we can’t take any materials with us.”
To obtain a material suitable for 3D printing, the team ground bits of meteorite into dust and mixed it with a small amount of polylactic acid – a type of biodegradable bioplastic – as well as a “regolith simulant”, a mix of Earth minerals meant to resemble the composition of the lunar surface.
Their design approximates the shape and size of Lego bricks, although the precision is difficult to re-create on this scale with 3D printing and required a lot of fine-tuning, according to the ESA.
The team said that for that reason, Lego brick shapes had become “a common test for this kind of project”.
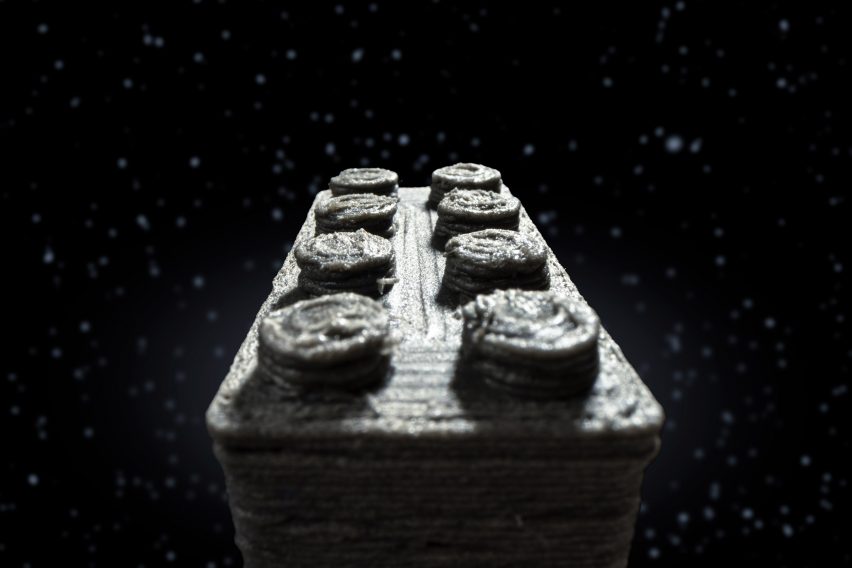
The blocks also work on the same principle as Lego, with tubes on the underside of the bricks interlocking with studs on the top of the bricks below. This connecting system creates a “clutch power” that makes Lego bricks so famously hard to pull apart.
“The result is amazing and whilst the bricks may look a little rougher than usual, importantly the clutch power still works, enabling us to play and test our designs,” said Cowley. “It was both fun and useful in scientifically understanding the boundaries of these techniques.”
The Lego Group has now put 15 of the ESA’s space bricks on display at its stores around the world, as the company says it hopes to inspire kids to build their own space shelters.
The Artemis programme has been running since 2017, with a crewed lunar landing scheduled for late 2026. The programme has also seen construction company ICON work on 3D-printing technology for the moon, fashion house Prada create space suits, and Lockheed Martin, General Motors and Goodyear develop a lunar vehicle.